Craftsmanship & ANOKHI
For decades, ANOKHI has drawn inspiration from Rajasthan’s rich craft heritage and collaborates with local artisans across a spectrum of traditional techniques. An interdependence of different hand skills is almost always needed to create an original ANOKHI piece. In addition to working with wood and brass block carvers, block printers and dyers, ANOKHI engages the dexterity of numerous other skilled workers – quilters, embroiderers and khari printers to name a few – to further enrich dyed and printed cloth.
Block Carving
Hand Block Carving is the first stage in the development of printed textiles. It lays the foundation for any hand printing, and therefore also underlies the basis of any later handicraft work incorporated in printed pieces, such as tassels or embroidery, making it an especially fundamental craft.
In itself, hand block carving is an immensely skilful & lengthy process. Wooden blocks are first planed and sanded for a smooth finish then whitened with a chalk paste to allow for tracing of the design. Working without the aid of any electrical machinery, carvers only use traditional hand tools, so intricate blocks such as this can take six days or longer to complete.

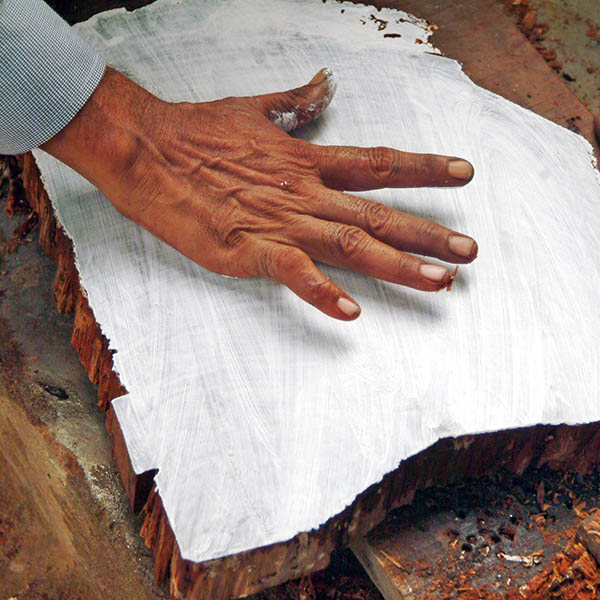

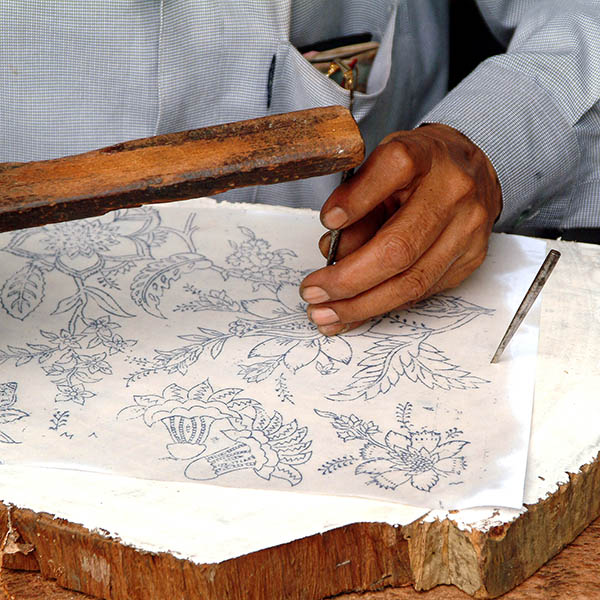

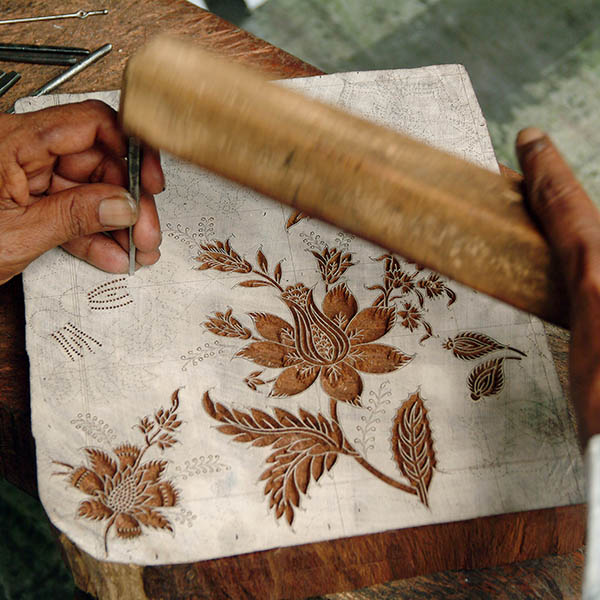
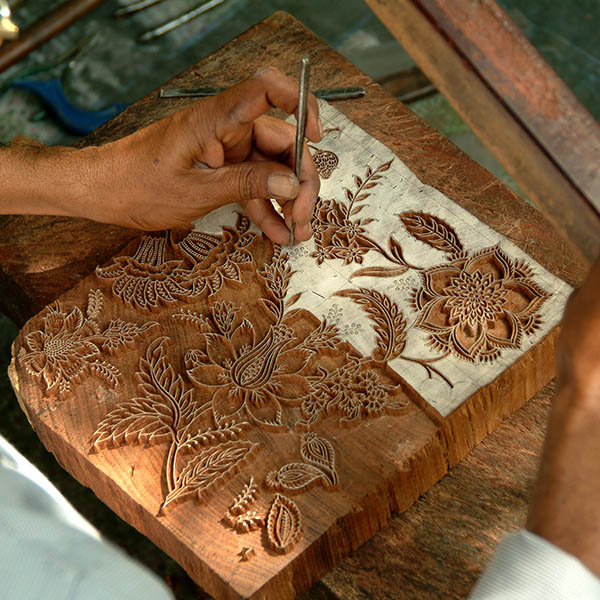

Patwa work
Mahesh ji is a highly-skilled patwa – an artisan specialising in threadwork. Taught by the elders of his family, he has mastered a variety of decorative finishes such as fundas (tassels), nadas (cords) and beadwork.
Here is a video of Mahesh ji creating fundas for an Anokhi evening dress.
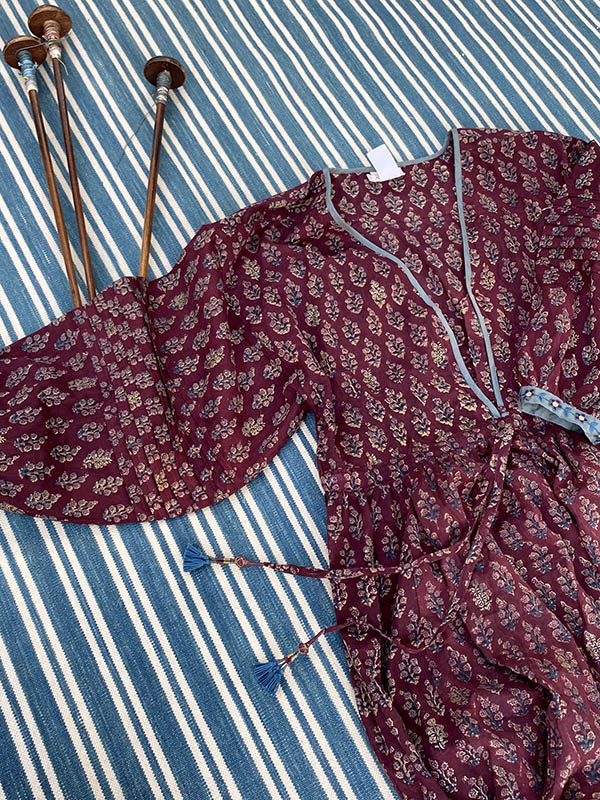
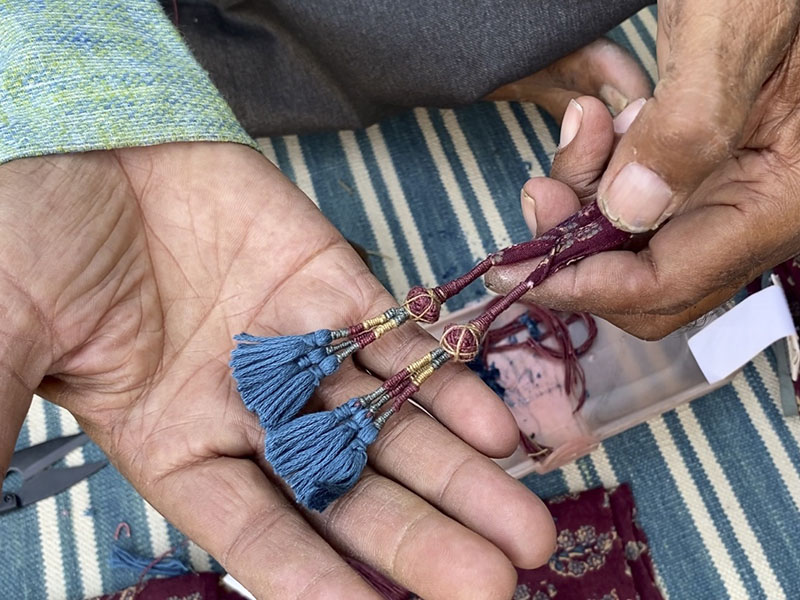
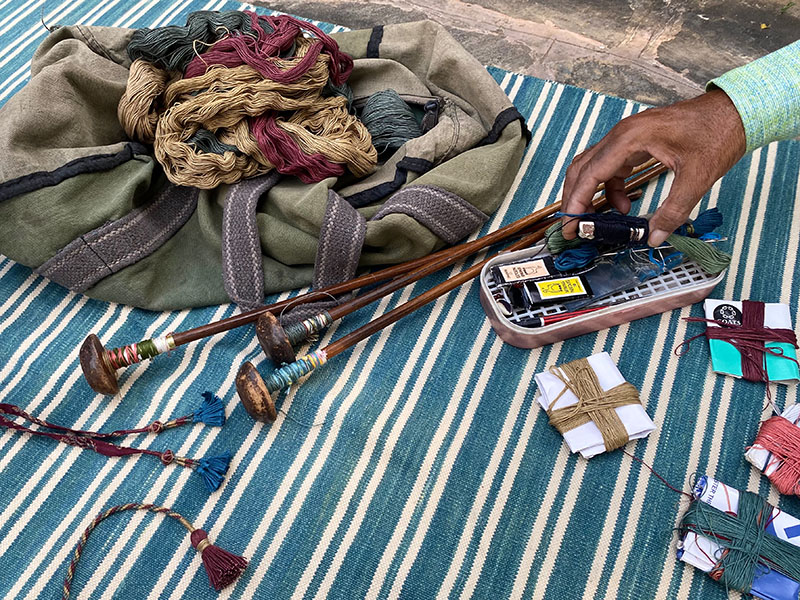
Keep an eye out for more videos of artisans sharing the intricate processes of their craftmanship, found in many Anokhi pieces.
Gold & Silver Print
Gold & silver printing is an embellishment frequently used on traditional Indian fabric.
Originally artisans painted or printed a pattern with ‘roghan’ gum paste then applied ‘varak’ gold or silver leaf, however few artisans still practice this method of application.
Today gold & silver printing requires the use of a brass tube with a stenciled base & metal plunger. The plunger is filled with paste & depressed, forcing a measured amount through the stencil onto the fabric. Using a muslin pouch, metallic powder is then dusted over the cloth to coat the design.
This type of printing offers a faster & less expensive imitation of embellishments such as zardozi metal embroidery & brocade weaves.